Maintenance Strategies for Prolonging Equipment Life in Oil Refineries
Maintenance Strategies for Prolonging Equipment Life in Oil Refineries
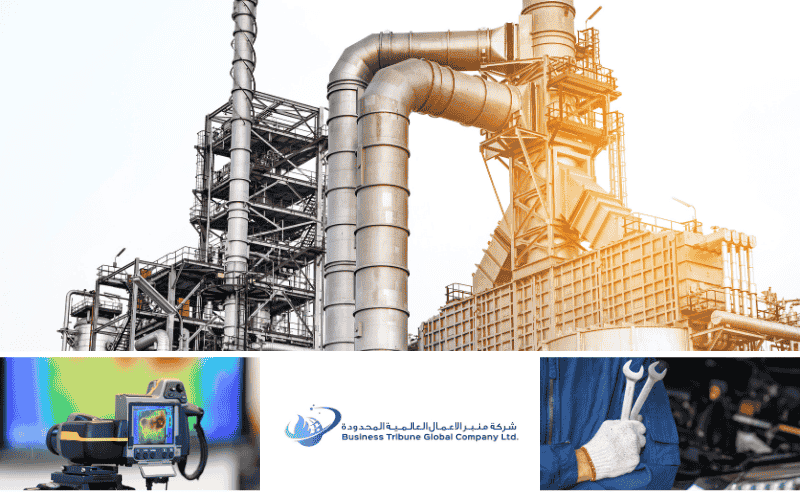
In the high-stakes environment of oil refineries, where equipment failure can lead to significant downtime and safety hazards, maintaining operational integrity is crucial. This article outlines essential maintenance strategies that can significantly prolong the life of equipment in oil refineries, reducing costs and enhancing safety.
Understanding the Challenges
Oil refineries operate under harsh conditions, with equipment subjected to extreme temperatures, pressures, and corrosive substances. The complexity of refinery operations necessitates a proactive approach to maintenance that can prevent unexpected failures and ensure continuous, safe operations.
Regular Maintenance Schedules
Planned Preventative Maintenance (PPM): Regularly scheduled inspections and maintenance are foundational to prolonging equipment life. By adhering to a PPM schedule, refineries can detect potential issues before they lead to equipment failure.
- Inspection and Testing: Routine checks of mechanical integrity for pumps, valves, and heat exchangers.
- Lubrication: Ensuring that all moving parts are properly lubricated to minimize wear and tear.
- Cleaning: Regular cleaning of equipment to prevent the buildup of residues that can lead to corrosion or efficiency loss.
Advanced Predictive Maintenance Techniques
Condition Monitoring: Implementing sensors and monitoring technologies to continuously assess the condition of equipment and predict when maintenance should be performed.
- Vibration Analysis: Tools that measure the frequency and amplitude of vibrations from machinery to identify imbalances or misalignments before they become problematic.
- Thermal Imaging: Using infrared cameras to detect unusual heat patterns that could indicate insulation failures, electrical faults, or poor lubrication.
Leveraging Technology for Maintenance Optimization
Integrated Maintenance Management Systems (IMMS): Utilizing advanced software solutions can help streamline maintenance processes, track performance, and prioritize maintenance tasks based on real-time data.
- Data Analysis: Using data collected from various sensors to analyze trends and predict equipment failures.
- Maintenance Planning: Advanced planning tools that help schedule maintenance activities around production demands to minimize downtime.
Training and Development
Investing in regular training programs for maintenance personnel is critical. Well-trained staff can better identify early signs of potential equipment failure and are more effective in applying complex maintenance protocols.
- Workshops and Seminars: Regular training sessions on the latest maintenance technologies and best practices.
- Certification Programs: Encouraging personnel to obtain certifications in areas like predictive maintenance and machinery lubrication.
Case Study: Success Story from a Leading Refinery
A leading oil refinery in Saudi Arabia implemented a holistic maintenance strategy that included upgrading their predictive maintenance technology and training staff extensively. The result was a 30% reduction in unscheduled downtime and a significant extension of equipment lifespan, contributing to safer operations and reduced operational costs.
Conclusion
Effective maintenance strategies are crucial for prolonging equipment life in oil refineries. By embracing a combination of preventative and predictive maintenance and investing in the latest technologies and training, refineries can achieve higher safety, efficiency, and profitability.