The Ultimate Guide to Reducing Downtime in Manufacturing Plants
The Ultimate Guide to Reducing Downtime in Manufacturing Plants
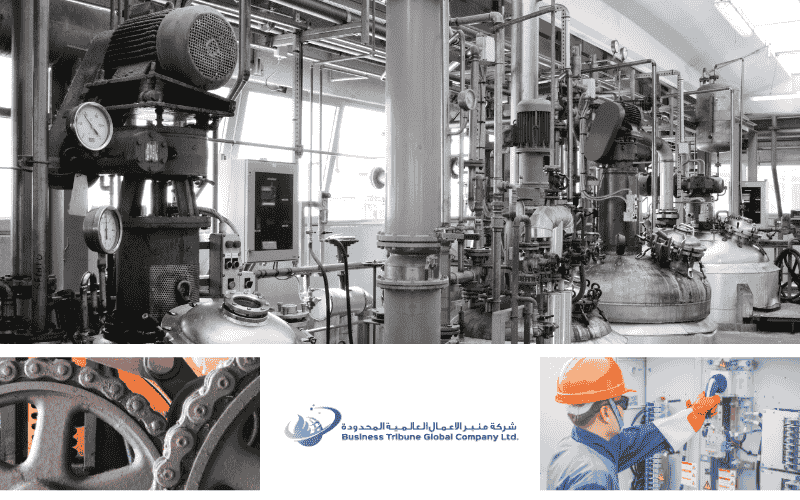
In the competitive world of manufacturing, downtime is a critical factor that can significantly impact productivity and profitability. This guide provides comprehensive strategies and best practices for minimizing downtime in manufacturing plants, ensuring continuous, efficient operations.
Understanding Downtime Causes
Identifying the root causes of downtime is the first step in effectively managing and reducing it. Common causes include equipment failure, operational inefficiencies, and human errors. By systematically addressing these areas, plants can enhance their operational resilience.
Preventive Maintenance Strategies
Scheduled Maintenance: Implementing a well-organized preventive maintenance schedule is essential to avoid unexpected machinery breakdowns.
- Routine Inspections: Regularly checking machinery for wear and potential issues.
- Component Replacements: Timely replacement of worn-out parts before they fail.
- Software Updates: Keeping automation software and operational technologies up to date to prevent malfunctions.
Predictive Maintenance Technologies
Leveraging Advanced Analytics: Utilizing data analytics and machine learning to predict when equipment is likely to fail and schedule maintenance accordingly.
- Vibration Analysis: Monitoring equipment vibrations to detect anomalies.
- Acoustic Monitoring: Using sound analysis to identify changes in machinery noise that indicate problems.
- Oil Analysis: Examining lubricants for contamination and chemical changes as early indicators of wear or failure.
Optimizing Operations Management
Streamlining Processes: Revising operational workflows to eliminate inefficiencies that can lead to downtime.
- Lean Manufacturing Principles: Applying lean principles to minimize waste and streamline production.
- Automated Monitoring Systems: Implementing systems that track production processes in real-time to quickly identify and address disruptions.
Training and Empowerment
Empowering employees with the right training and tools is crucial for reducing downtime. Workers who are well-trained in both operational procedures and troubleshooting can often prevent or quickly resolve issues that might otherwise lead to extended downtime.
- Skill Development Programs: Regular training sessions on new technologies and methods.
- Empowerment Initiatives: Programs that encourage workers to take initiative and make decisions that prevent downtime.
Case Study: Efficiency Gains in a Local Manufacturing Plant
A local Saudi manufacturing plant recently overhauled its maintenance and operations protocols, integrating predictive maintenance tools and refining its operational workflows. The result was a 40% reduction in unscheduled downtime and a marked improvement in overall plant efficiency.
Conclusion
Reducing downtime in manufacturing plants requires a multi-faceted approach that includes regular maintenance, adoption of new technologies, process optimization, and employee training. By implementing these strategies, plants can not only decrease downtime but also boost productivity and operational efficiency.